L’outil 8D, reconnu pour son efficacité dans la résolution de problèmes complexes, est une méthode structurée principalement utilisée dans la gestion de la qualité. Cet outil, développé à l’origine par Ford Motor Company, s’est imposé comme un standard dans de nombreuses industries pour son approche systématique et rigoureuse. Il se distingue par son processus en huit étapes distinctes qui guident les équipes à travers toutes les phases de la résolution de problèmes, depuis l’identification initiale du problème jusqu’à sa résolution définitive et la prévention de sa récurrence.
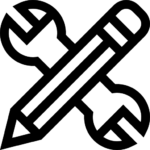
L’importance de l’outil 8D dans les démarches qualité réside dans sa capacité à identifier, corriger et, surtout, à prévenir les problèmes de long terme. En encourageant une analyse approfondie des causes racines, il assure que les corrections ne sont pas simplement temporaires ou superficielles. Cela conduit à des améliorations significatives et durables de la qualité des produits ou des services. De plus, l’outil 8D favorise la collaboration et la communication au sein des équipes, éléments essentiels pour une culture d’entreprise axée sur la qualité. Sa mise en œuvre systématique permet non seulement de résoudre efficacement les problèmes, mais aussi de renforcer la confiance des clients et d’améliorer l’image de marque de l’entreprise. En somme, l’outil 8D est un pilier dans les stratégies de gestion de la qualité, indispensable pour toute organisation souhaitant optimiser ses processus et garantir l’excellence de ses produits ou services.
Comprendre l’Outil 8D
Qu’est-ce que l’Outil 8D ?
La méthode 8D commence par la formation d’une équipe (D1), suivie de la définition précise du problème (D2). Une fois le problème clairement défini, l’équipe développe et met en œuvre un plan d’actions temporaires pour contenir les effets du problème (D3). L’étape suivante, D4, consiste à trouver la cause racine du problème, ce qui est crucial pour empêcher sa récurrence. Après avoir identifié la cause racine, l’équipe choisit et vérifie les actions correctives à long terme (D5), puis les met en œuvre (D6). L’avant-dernière étape (D7) implique la mise en place de systèmes pour prévenir la réapparition du problème. Finalement, l’équipe est félicitée et reconnue pour son travail (D8), un élément important pour maintenir la motivation et l’engagement.
Le principal objectif de l’outil 8D est de résoudre les problèmes de manière efficace et méthodique, en éliminant les causes profondes pour éviter leur répétition. Cet outil est particulièrement utile dans les environnements où la qualité et la fiabilité des produits sont primordiales. Il encourage une approche collaborative et interdisciplinaire, en rassemblant différentes compétences et perspectives pour une analyse approfondie du problème.
Les avantages de l’utilisation de l’outil 8D dans la gestion de la qualité sont multiples. Il permet une approche standardisée et reproductible de la résolution de problèmes, assurant ainsi une certaine cohérence dans les processus de qualité à travers l’organisation. En se concentrant sur les causes racines, les entreprises évitent les solutions temporaires et superficielles, favorisant des améliorations durables. De plus, l’outil 8D renforce la collaboration interne et améliore la communication entre les départements, ce qui est essentiel pour une culture d’entreprise forte et centrée sur la qualité.
L’Histoire et l’Évolution de l’Outil 8D
L’origine de la méthode 8D remonte aux années 1980. Elle a été développée par Ford Motor Company en réponse à une série de problèmes de qualité rencontrés dans leur processus de production. Ford a conçu cette méthode pour améliorer la qualité de ses produits et pour répondre aux exigences de ses clients, notamment en termes de fiabilité et de performance. L’outil 8D a été rapidement adopté par d’autres industries, attirant l’attention pour sa capacité à apporter des solutions durables et efficaces aux problèmes complexes.
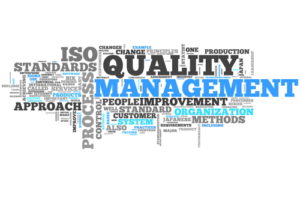
Au fil des années, l’outil 8D a évolué pour intégrer des concepts de diverses disciplines, comme le Six Sigma et le Lean Manufacturing, rendant la méthode encore plus robuste et efficace. Sa flexibilité lui a permis d’être adopté dans une multitude de secteurs, allant de l’automobile à l’aérospatiale, en passant par la santé et l’électronique. Cette universalité témoigne de sa force en tant qu’outil de résolution de problèmes.
Le développement de l’outil 8D est également lié à l’évolution des normes de qualité internationales, comme l’ISO 9001. Ces normes mettent l’accent sur l’amélioration continue, un principe au cœur de la méthode 8D. Ainsi, l’adoption de l’outil 8D par les entreprises est souvent vue comme un pas en avant vers la conformité avec ces normes internationales et une preuve de leur engagement envers la qualité.
En conclusion, l’outil 8D représente plus qu’une simple méthode de résolution de problèmes. C’est un pilier dans la stratégie de gestion de la qualité d’une entreprise, un symbole de son engagement envers l’excellence et l’amélioration continue. Sa capacité à s’adapter à différents environnements et à intégrer des concepts d’autres disciplines en fait un outil polyvalent et inestimable pour toute organisation soucieuse de la qualité de ses produits et services.
Les Huit Étapes du Processus 8D
D1 à D4 : Identifier et Contenir le Problème
Les premières étapes de l’outil 8D, de D1 à D4, sont cruciales pour poser les bases d’une résolution de problème efficace. La première étape, D1, consiste à former une équipe. Cette équipe doit être composée de membres ayant différentes compétences et perspectives, ce qui est essentiel pour une analyse complète du problème. Une fois l’équipe formée, la deuxième étape, D2, implique de définir et de décrire le problème. Cette description doit être claire, concise et basée sur des données factuelles. Il est important d’éviter les suppositions ou les généralisations à ce stade.
La troisième étape, D3, consiste à développer un plan de confinement intérimaire. L’objectif ici est de limiter l’impact du problème en cours d’investigation. Cette étape peut impliquer des mesures temporaires telles que la mise en quarantaine des produits défectueux ou la modification temporaire des processus de production. Le confinement aide à prévenir l’aggravation du problème tout en donnant à l’équipe le temps nécessaire pour analyser la situation.
D4, la quatrième étape, est l’une des plus critiques : déterminer la cause principale du problème. Cette étape nécessite une analyse approfondie et peut s’appuyer sur diverses techniques, comme le diagramme d’Ishikawa ou l’analyse des cinq pourquoi. Identifier la cause principale est crucial pour s’assurer que les solutions apportées seront efficaces à long terme.
Un exemple d’application de ces étapes peut être trouvé dans l’industrie manufacturière, où une équipe de qualité pourrait être formée pour résoudre un problème de défauts récurrents dans un produit. Après avoir défini le problème en détail et mis en place des mesures de confinement, comme l’arrêt de la production ou la mise de côté des lots affectés, l’équipe utiliserait des outils d’analyse pour identifier la cause principale, comme un défaut dans une machine ou une erreur dans la procédure de production.
D5 à D8 : Analyser, Corriger et Prévenir
Les étapes D5 à D8 de l’outil 8D se concentrent sur l’analyse approfondie du problème, la mise en œuvre de solutions, et la prévention de récurrence. La cinquième étape, D5, implique de choisir et de vérifier les actions correctives permanentes. Une fois la cause principale identifiée, il est essentiel de développer des solutions qui adressent cette cause de manière efficace. Ces solutions doivent être testées pour vérifier leur efficacité avant d’être pleinement implémentées.
D6, la sixième étape, est la mise en œuvre des actions correctives. Cette étape va au-delà de la simple application des solutions ; elle implique également de s’assurer que ces solutions sont intégrées dans les processus standards de l’entreprise et qu’elles sont efficaces sur le long terme. L’implication de toutes les parties prenantes est cruciale à cette étape pour garantir une transition en douceur et une acceptation des changements.
L’étape D7 vise à prévenir la récurrence du problème. Cela implique souvent des modifications des processus, des formations pour les employés, et parfois des changements dans la culture organisationnelle. L’objectif est de s’assurer que le problème, une fois résolu, ne se reproduira pas.
Enfin, D8 est une étape souvent négligée mais importante : féliciter l’équipe. Reconnaître les efforts et les réussites de l’équipe renforce la motivation et encourage une culture d’amélioration continue au sein de l’organisation.
Dans un contexte d’application, prenons l’exemple d’une entreprise de logistique confrontée à des retards répétés dans les livraisons. Après avoir identifié la cause principale (D4) comme étant un problème dans la planification des itinéraires, l’équipe pourrait développer une nouvelle stratégie de planification (D5) et la
mettre en œuvre (D6). Pour prévenir la récurrence (D7), des formations régulières pourraient être organisées pour les planificateurs d’itinéraires et des revues périodiques des processus pourraient être mises en place. Enfin, la reconnaissance des efforts de l’équipe (D8) contribuerait à maintenir un haut niveau d’engagement et d’efficacité.
Utilisation de l’audit 8D
En conclusion, les étapes D1 à D4 et D5 à D8 de l’outil 8D constituent une approche complète et structurée pour la résolution de problèmes. Elles permettent non seulement de résoudre les problèmes de manière efficace, mais aussi de mettre en place des mesures pour éviter leur réapparition, jouant ainsi un rôle crucial dans les démarches d’amélioration continue au sein des organisations.
Une méthode incontournable à utiliser lorsque cela est nécessaire
En conclusion, l’outil 8D s’est établi comme une méthode incontournable dans le domaine de la gestion de la qualité. Par son approche structurée et sa méthode en huit étapes, il offre aux entreprises un cadre clair et efficace pour résoudre les problèmes les plus complexes. De la formation d’une équipe dédiée à la reconnaissance de ses efforts, chaque étape de l’outil 8D est conçue pour aborder les problèmes de manière exhaustive, en se concentrant sur l’élimination des causes racines et en évitant les solutions temporaires.
L’efficacité de l’outil 8D ne réside pas seulement dans sa capacité à résoudre des problèmes spécifiques, mais aussi dans son rôle crucial dans l’instauration d’une culture d’amélioration continue au sein des organisations. En intégrant l’outil 8D dans leurs processus, les entreprises peuvent non seulement améliorer la qualité de leurs produits et services, mais également renforcer la confiance et la satisfaction de leurs clients. De plus, l’outil favorise la collaboration interne, améliore la communication entre les départements et contribue à une meilleure compréhension des processus opérationnels.
Nous encourageons vivement les dirigeants et les responsables de qualité dans les TPE et PME à adopter l’outil 8D. Son intégration peut sembler exigeante au départ, mais les bénéfices à long terme en termes d’efficacité opérationnelle, de réduction des coûts et d’amélioration de la qualité sont indéniables. En adoptant l’outil 8D, votre entreprise ne se contente pas de résoudre des problèmes ; elle adopte une philosophie de qualité qui est synonyme de durabilité et de succès dans le monde des affaires compétitif d’aujourd’hui.